
In fluid mechanics and engineering, a check valve is vital. It controls the flow of liquids or gases and is used inside pipelines and structures. Its layout is simple but ingenious. The check valves regulate the flow of floats, preventing undesirable backflow and guaranteeing the easy motion of materials via the supposed path.
Have you ever contemplated how water can float via pipes in a single route without reversing its course? Or why are you sure structures preserve stress and integrity even if disconnected? The solution lies in the workings of a test valve. But what precisely is that device, and how does it do one of these feats?
A test valve, additionally called a non-go back valve or one-manner valve, has capabilities as a gatekeeper for fluid or fuel line float. Its mechanism lets in motion in a single route even as blockading any attempt at reversal. This essential idea applies in lots of industries. It’s used in family plumbing structures. Also, in complicated business processes. Understanding the capability of a test valve is essential. It’s widespread in fluid dynamics, engineering, and machine layout.

Types of Check Valves
Types of check valves are as follows:
Swing Check Valves:
Swing test valves use a swinging disc to manipulate fluid or fuel waft. When strain is better on one side, the disc swings open, permitting waft. When strain equalizes or reverses, the disc swings back, stopping
backflow.
Lift Check Valves:
Lift check valves view more carry a disc or piston to allow waft in a single direction. When strain decreases, the disc settles, blockading waft and stopping backflow. They’re not unusual places in vertical waft applications.
Ball Check Valves:
Ball check valves are characterized by a round ball that acts as a barrier. Higher strain pushes the ball aside, permitting a waft. When strain changes, the ball returns, sealing the valve to save you backflow.
Diaphragm Check Valves:
Diaphragm check valves use a bendy diaphragm to manipulate the waft. Higher strain flexes the diaphragm, permitting waft. When strain changes, the diaphragm returns, sealing the valve to save you backflow.

Benefits of Using Check Valves·
Check valves keep waft direction, stopping infection and making sure gadget integrity.· They mitigate harm from strain surges and leaks, selling protection and reliability. With low protection and cost-effectiveness, they beautify the gadget’s overall performance and efficiency. Found in numerous industries, test valves facilitate fluid or gas waft manipulation. They make sure operational requirements are met.
They save you water hammer effects, decreasing pressure on pipelines and equipment. Check valves provide short reaction times. This is essential for approving applications. Especially the ones requiring speedy waft manipulation adjustments. Their compact layout allows for smooth integration into various gadget configurations.
Applications of Check Valves
Check valves and discover numerous programs in regular systems. Plumbing usually uses them to prevent water from flowing backward, ensuring it acts in a single path only. Test valves are essential for heating and cooling systems. They preserve the float of fluids inside the preferred path, which prevents harm and facilitates the preservation of performance. They’re additionally crucial in industries like oil and fuel lines.
Check valves to prevent backflow and preserve stress in pipelines, guaranteeing protection and performance in transportation. Test valves are also used in scientific equipment and are imperative to car systems. Many programs depend upon them, where controlling fluid or gas float is vital.
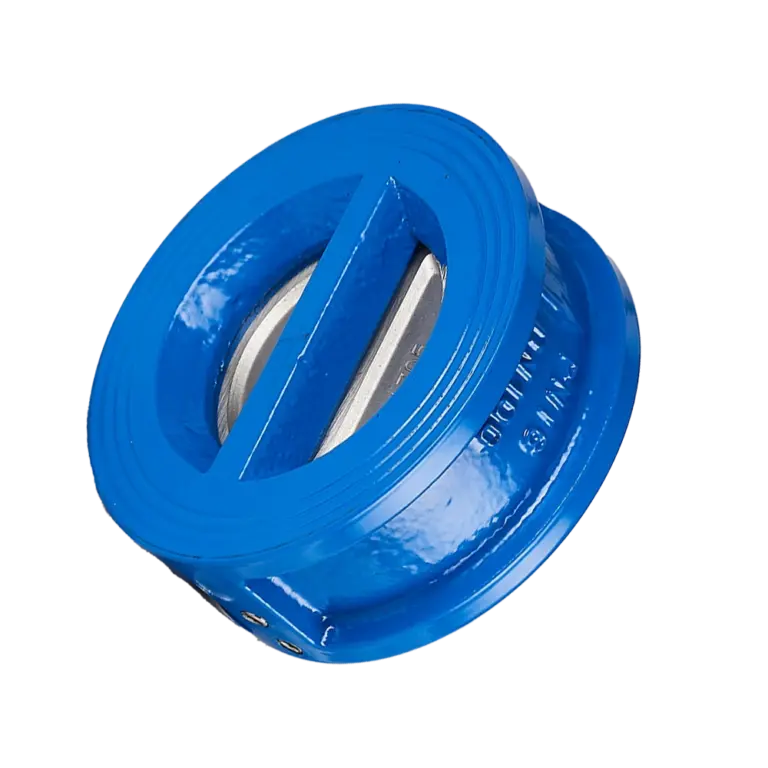
Common Issues with Check Valves
Common problems with test valves can arise. These encompass troubles like fouling. Fouling occurs while particles or sediment accumulates and obstructs the valve’s movement. It results in reduced performance. Another problem is the opposite float. Improper setup or put and tear can cause this problem. It compromises machine integrity while fluid or fuel lines flow inside the incorrect path. Additionally, test valves might also reveal leaking.
Sealing screw-ups also can arise over time. Especially in high-stress systems, renovation or replacement can be necessary. Ensuring the proper setup is essential. Regular inspection is likewise crucial. Maintenance can assist mitigate those problems and extend the lifespan of test valves in various applications.
Choosing the Right Check Valve
When choosing the appropriate test valve, numerous elements have to be considered. This guarantees top-quality overall performance and compatibility with the machine. Testing the float characteristics, including float charge and stress necessities, is vital. This facilitates deciding on a valve that can cope with the expected situations. Certain substances can be more appropriate to unique programs. They face up to corrosion or chemical harm extra effectively.
Additionally, elements like setup orientation matter. Size and connection should additionally. This guarantees the machine’s right match and capability. The surroundings and working situations ought to be considered. These elements help make a knowledgeable selection when choosing the proper test valve for the application.
Conclusion
Understanding and looking at valves is vital in fluid mechanics and engineering. They make sure one-manner glides, stopping backflow and contamination. Various styles of looking at valves are available. These encompass swing, lift, ball, and diaphragm take a look at valves. Each is ideal for particular applications. Their significance throughout industries is evident.
Despite unusual place troubles like fouling and leaks, the proper setup and renovation are key. Considering glide traits is essential. The fluid kind of subjects, too. Selecting the appropriate take-look at the valve can optimize the machine’s overall performance and safety.